摘要:本文论述了高炉炼铁炉内操作与炉渣MgO/Al2O3的关系,介绍了我国高炉2015年炉渣MgO/Al2O3的基本情况,论述了炉渣稳定性与MgO/Al2O3的关系,论述了MgO/Al2O3对高炉炼铁的价值,并提出了我国高炉炼铁优化MgO/Al2O3的几点认识。
关键词:炉内操作炉渣稳定性;优化MgO/Al2O3的价值
1 高炉炉内操作与炉渣的MgO/Al2O3
保持高炉炉况稳定顺行是高炉实现低成本低燃料比炼铁的先决条件,而高炉炉况的稳定顺行是靠炉料质量和良好的炉内操作实现的。炉内操作通常通过执行装料制度、送风制度、热制度和造渣制度得到保障的。现代高炉操作装料制度的优化是通过多环布料使用一定的档位,调整形成“平台+小漏斗”的炉喉煤气分布状态[1];现代高炉操作送风制度的优化是使风量和风速形成煤气流在燃烧带的合理分布,达到炉腹煤气量指数与炉料质量相适应,保持高炉下部顺行;现代高炉操作的热制度需要炉缸有足够的热量使炉缸既不凉又不过热的适宜温度,保持炉缸稳定的热状态;现代高炉操作的的造渣制度需要做到既要适应原燃料条件和生铁质量的要求,又要做到当炉渣成分和炉温波动时,保持炉渣具有良好的化学稳定性和物理稳定性,实现炼好铁首先要炼好渣。在高炉炉内操作四大制度中,造渣制度可以说是最重要的炉内操作制度。
高炉炼铁造渣制度的优化主要是通过控制炉渣碱度和炉渣成分在一个适宜的范围内保持炉渣具有良好的流动性和脱硫脱碱效果,而炉渣的流动性和脱硫脱碱效果均与MgO/Al2O3直接相关。因此探索研究炉渣的MgO/Al2O3对搞好炉内操作和保持高炉长期稳定顺行具有重要价值。
2 我国高炉炼铁MgO/Al2O3的现状与发展趋势
今年初,笔者对2015年我国大小不同容积275座高炉的主要操作指标作了一个较详细的统计[2],其中包括不同炉容低MgO/Al2O3的状况(见表1)。
表1 2015年我国高炉低MgO/Al2O3炼铁的状况
|
炉容
|
高炉炉渣成分(%)
|
R
|
渣铁比
|
烧结矿成分(%)
|
企业名称
|
m3
|
Al2O3
|
MgO
|
MgO/Al2O3
|
CaO/SiO2
|
Kg/t
|
Al2O3
|
MgO
|
安阳钢铁
|
500
|
15.05
|
6.58
|
0.437
|
1.30
|
327
|
-
|
-
|
(黑)建龙
|
530
|
15.05
|
6.58
|
0.437
|
1.09
|
-
|
-
|
-
|
沙钢
|
480
|
15.88
|
7.82
|
0.492
|
1.24
|
-
|
-
|
-
|
沙钢
|
480
|
15.75
|
7.71
|
0.489
|
1.26
|
-
|
-
|
-
|
沙钢
|
480
|
15.85
|
7.77
|
0.489
|
1.24
|
-
|
-
|
-
|
沙钢
|
480
|
15.92
|
7.76
|
0.487
|
1.23
|
-
|
-
|
-
|
淮钢
|
450
|
14.95
|
7.11
|
0.476
|
1.20
|
355
|
1.93
|
1.55
|
淮钢
|
450
|
14.72
|
7.15
|
0.486
|
1.20
|
355
|
1.93
|
1.55
|
淮钢
|
580
|
14.86
|
7.10
|
0.478
|
1.21
|
355
|
1.93
|
1.55
|
淮钢
|
580
|
14.92
|
7.05
|
0.473
|
1.21
|
355
|
1.93
|
1.55
|
宝钢不锈
|
750
|
15.59
|
7.16
|
0.459
|
1.21
|
318
|
1.97
|
1.61
|
衡管
|
1080
|
16.04
|
7.08
|
0.441
|
1.16
|
-
|
2.16
|
1.86
|
湘钢
|
1080
|
15.52
|
7.69
|
0.495
|
1.19
|
364
|
-
|
-
|
长钢
|
1080
|
15.36
|
5.79
|
0.377
|
1.20
|
372
|
-
|
-
|
长钢
|
1080
|
15.52
|
5.83
|
0.376
|
1.20
|
372
|
-
|
-
|
安阳钢铁
|
2200
|
15.08
|
6.23
|
0.413
|
1.31
|
353
|
-
|
-
|
邯钢
|
2000
|
15.75
|
7.28
|
0.462
|
1.27
|
328
|
-
|
-
|
邯钢
|
2000
|
15.77
|
7.32
|
0.464
|
1.27
|
333
|
-
|
-
|
湘钢
|
1800
|
15.52
|
7.44
|
0.479
|
1.20
|
365
|
-
|
-
|
湘钢
|
1800
|
15.63
|
7.50
|
0.480
|
1.21
|
367
|
1.86
|
1.86
|
莱钢
|
1880
|
15.36
|
5.04
|
0.328
|
1.20
|
410
|
2.17
|
1.06
|
莱钢
|
1880
|
15.19
|
4.92
|
0.324
|
1.22
|
413
|
2.17
|
1.06
|
武钢
|
2200
|
14.87
|
7.29
|
0.490
|
1.18
|
333
|
1.78
|
1.77
|
宁波钢铁
|
2500
|
15.90
|
7.15
|
0.450
|
1.24
|
298
|
1.71
|
1.53
|
宁波钢铁
|
2500
|
15.75
|
7.18
|
0.456
|
1.25
|
297
|
1.72
|
1.53
|
宝钢不锈
|
2500
|
15.69
|
6.60
|
0.421
|
1.12
|
322
|
1.96
|
1.63
|
沙钢宏发
|
2500
|
15.30
|
7.34
|
0.480
|
1.25
|
310
|
1.76
|
1.60
|
沙钢宏发
|
2500
|
15.12
|
7.26
|
0.480
|
1.24
|
308
|
1.76
|
1.60
|
沙钢宏发
|
2500
|
15.18
|
7.29
|
0.480
|
1.24
|
309
|
1.76
|
1.60
|
梅山钢铁
|
3200
|
15.69
|
7.54
|
0.481
|
1.20
|
305
|
1.86
|
1.65
|
邯钢
|
3200
|
15.59
|
7.39
|
0.474
|
1.27
|
339
|
-
|
-
|
莱钢
|
3200
|
15.44
|
4.75
|
0.308
|
1.23
|
410
|
2.15
|
0.99
|
安阳钢铁
|
4800
|
15.60
|
6.74
|
0.432
|
1.23
|
297
|
-
|
-
|
梅山钢铁
|
4070
|
15.75
|
7.26
|
0.461
|
1.21
|
303
|
1.86
|
1.64
|
跨入新世纪以来,国内外炼铁工作者在实现低成本、低燃料比高炉炼铁的实践中,开始重视降低炉渣的MgO/Al2O3,早在2005年,我国武钢和福建三明、三安钢铁公司的高炉冶炼,就实现了低MgO/Al2O3高炉操作,武钢6#高炉炉渣的Al2O3高达17.0%,将MgO/Al2O3降到低于0.60的水平[3],三明钢铁公司5#高炉、三安钢铁公司1#、2#高炉率先将MgO/Al2O3降低到0.41和小于0.20的水平[4]。说明十年前在我国己有少数几座高炉实现低了MgO/Al2O3的高炉操作。由表1可见,十年后的2015年,我国不完全统计即有近40座高炉实现了低于0.50的低MgO/Al2O3操作,且高炉容积不分大小,都有低MgO/Al2O3操作的范例。
国内外炼铁工作者为什么要追求低MgO/Al2O3操作呢?降低炉渣的MgO/Al2O3要从降低烧结矿的MgO含量入手,烧结矿的生产实践证明,MgO不是烧结矿质量的正能量,它恰恰是烧结矿质量的负能量,提高烧结矿的MgO含量,不仅会降低其品位、还会降低其冷强度和还原性,从烧结矿的产质量和低成本出发,生产自然MgO烧结矿为佳。但这对高炉炼铁来说不那么简单,降低了烧结矿的MgO,也就降低了炉渣的MgO,炉渣的MgO降低了即降低MgO/Al2O3,会影响炉渣的流动性和脱硫脱碱效果,所以一般高炉操作工不轻易降低炉渣的MgO/Al2O3,高炉炉内操作要实现低MgO/Al2O3,需要在理论上搞清楚炉渣的性能与MgO/Al2O3的关系。这是我国高炉炼铁要普遍实现低MgO/Al2O3操作的一个重要理论问题。
3 高炉渣的稳定性与其镁铝比(MgO/Al2O3)
3.1 炉渣的稳定性
炉渣的稳定性是炉渣的综合性能,当炉缸温度或炉渣成分波动时保持炉渣的溶化性温度和粘度稳定的能力。高炉渣的稳定性又可分为热稳定性和化学稳定性两种性能,当炉缸温度正常范围内波动时,炉渣粘度不会进入长渣向短渣转折区或溶化性温度不发生明显变化的,称为炉渣的热稳定性;当炉渣成分波动时能保持上述特征稳定的能力称为炉渣的化学稳定性。因此,广大炼铁工作者都十分重视高炉渣的性能,公认的炼好铁必须炼好渣,保持炉渣的热稳定性和化学稳定性。
3.2 炉渣稳定性与MgO/Al2O3
大量的研究和生产实践证明[5],高炉炉渣的稳定性与MgO/Al2O3比相关。随着铁矿资源的开发利用,铁矿石的Al2O3含量有不断升高的趋势,造成高炉渣中的Al2O3含量不断上升,有些企业炉渣的Al2O3含量高达15%~17%, Al2O3含量的升高会影响炉渣的流动性即渣粘度要增大,而炉渣粘度对高炉冶炼进程有很大的影响,粘稠的初渣和中渣,会阻碍料柱中焦炭孔隙的气流通道,妨碍高炉下部顺行和强化,容易引起高炉难行和下部悬料;粘稠的终渣容易造成炉缸堆积,烧坏风口和渣铁不分等,影响高炉正常生产〔6〕。解决高炉渣粘稠的问题,炼铁工作者的经验往往是提高炉渣MgO的含量,因为MgO可以改善炉渣的流动性,故炉渣的MgO/Al2O3比是一个有价值的数据,通常,当冶炼制钢生铁高炉渣的Al2O3为8~15%时,MgO为5~10%,MgO/Al2O3的值相当0.625~0.667,这个比值合理不合理,能不能优化?这不仅对把握好炉渣性能,对高炉顺行有利,同时也会有利于烧结和炼铁成本的降低。
3.3 优化高炉炼铁MgO/Al2O3的理论分析
炉渣的融化温度和粘度与炉渣的四元系相图密切相关,高炉渣的低熔化温度和低粘度区为黄长石和镁蔷薇辉石区域,高炉渣的四元系渣相状态图列于图1,当渣碱度(CaO/SiO2)=0.7~1.3时,是炉渣熔化温度最低的区域,渣碱度低于或高于该区域,炉渣的融化温度都会升高。当Al2O3=15%和20%时,四元系等熔化和等粘度曲线列于图2和图3及图4.
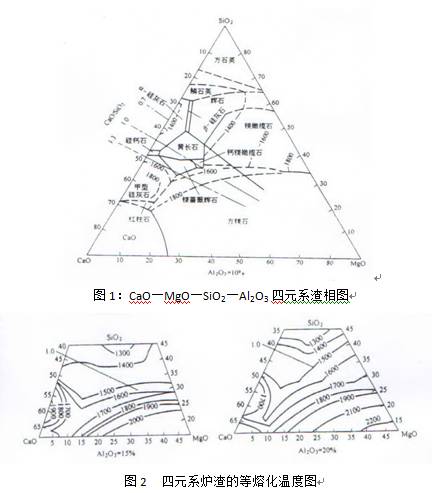
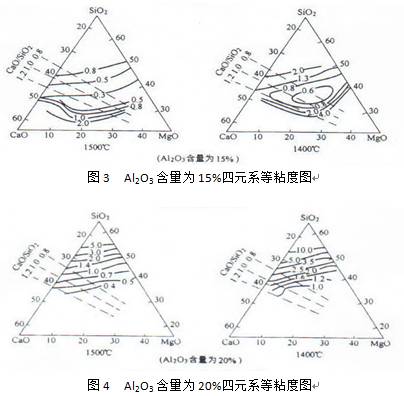
当Al2O3的含量由10%升高到15%~20%时,碱度升高对熔化温度的影响减小了,由图2可见,低熔化温度区扩展了[7],因此炉渣的Al2O3含量升高,不会造成低熔化温度区缩小。
高炉渣的正常粘度范围在0.5~2.0pa·s之间,由图3的四元系粘度曲线可见,高炉渣的粘度适宜区与熔化温度适宜区比较是基本一致的,炉渣粘度随其温度升高而下降,故保持炉缸温度>1400℃是确保炉渣低熔化和低粘度的重要条件。炉渣的MgO含量对其粘度有很大影响,当碱度在0.8~1.25的范围内,MgO含量在5%左右时可以使CaO<35%的低碱度渣粘度明显下降,而且融化温度也明显降低;当MgO含量>9%~10%时,可以使低粘度区明显扩大,但粘度特征明显出现由“长渣变短渣”的转折点,且此时熔化温度也开始升高,说明在适宜的碱度范围内,提高MgO含量对改善炉渣的性能既有有利的的因素,也有不利的影响。这就是为什么国内外不少企业实行低MgO高Al2O3即合理的MgO/Al2O3高炉炼铁理论的根据和道路所在, MgO含量对粘度曲线的影响见图5.

4 优化高炉炼铁MgO/Al2O3的价值
随着铁矿资源的开发,铁矿石的Al2O3含量有不断升高的趋势,引起炉渣
Al2O3的含量升高,保持炉渣的MgO/Al2O3值,必然要提高烧结矿的MgO含量,提高烧结矿的MgO含量,不仅会降低烧结矿的还原性和转鼓指数。国内外公认数据是,烧结矿每提高1%的MgO含量,会降低5%的900℃还原性和3%的转鼓指数。为了提高烧结矿MgO含量,不仅要加入白云石之类的含MgO矿物,会降低烧结矿的含铁品位,烧结矿每提高1%的MgO含量,会降低1.36%的品位,增加40kg渣量,在60美元/t的矿价下,烧结矿的成本将会上升40元(人民币)以上,为实现低成本、低燃料比为中心的炼铁方针,不能随铁矿粉的Al2O3含量提高而不断增加MgO含量,而是要适当控制高炉渣的MgO/Al2O3。当炉渣的Al2O3含量不高于17.0%的条件下,MgO/Al2O3可控制在0.45左右的水平,炉渣的MgO可控制在不高于8.0%的水平;当炉渣的Al2O3含量不高于15.0%的条件下,炉渣的MgO可控制在不高于7%的水平,相应地烧结矿MgO含量可控制在不高于1.6~1.8%的水平,这样优化高炉炼铁的MgO/Al2O3,既可以提高炉内操作水平,也有利于提高企业炼铁的低成本竞争力。
5 结论性意见
通过以上介绍,论述和分析可以得出以下结论性意见:
1) 高炉炼铁要保持稳定顺行,应十分重视炉渣的稳定性,高炉渣的稳定性与渣的MgO/Al2O3相关。
2) 高炉渣适宜的碱度在0.8~1.25范围,由四元渣相图黄长石和镁蔷薇辉石是高炉渣低熔化温度和低粘度区域,当炉渣Al2O3含量由10%提高到15%~20%时,低熔化温度区扩展了,5%左右MgO含量有利于降低炉渣的粘度和熔化温度;当MgO含量>9%~10%,低粘结区会明显扩大,但炉渣“短渣”的转折点明显出现,且熔化温度也开始升高。
3) 当炉渣的Al2O3含量不超过15%和17%炉缸温度不低于1460℃的条件下,相应地MgO含量可控制在不高于7%和8%的水平,烧结矿的MgO可控制在1.6%~1.8%的水平。
4) 国内外大中小型各类高炉炉渣均有采用低MgO/Al2O3冶炼操作的范例,
低MgO/Al2O3有利于提高炉内操作水平,有利于改善烧结矿的质量、降低渣量和燃料比、有利于降低生铁成本, 提高企业成本竞争力。
6 参考文献
[1] 柳袆.邯宝3200m3高炉低燃料比操作技术优化[J].第十四届全国大高炉炼铁学术年会论文集,甘肃嘉峪关,2013.9(294).
[2] 许满兴.2015年全国高炉炼铁主要操作指标分析[J].炼铁交流.2016(3),1-14.
[3] 杨志泉.武钢高炉渣中Al2O3含量异常升高原因与对策[J].炼铁.2006.No:1(20).
[4] 郭志刚.三安高炉高Al2O3炉渣冶炼实践[J].炼铁.2006.No:1(25).
[5] 沈峰满,等.国内外高炉渣镁铝比的对比分析[J].中国冶金报.2015年8月27日06版.
[6] 周传典主编.高炉炼铁生产技术手册[M].造渣过程及造渣性能.北京:冶金工业出版社2002.8(118-126).